Transform your eCommerce strategy with 3D & AR
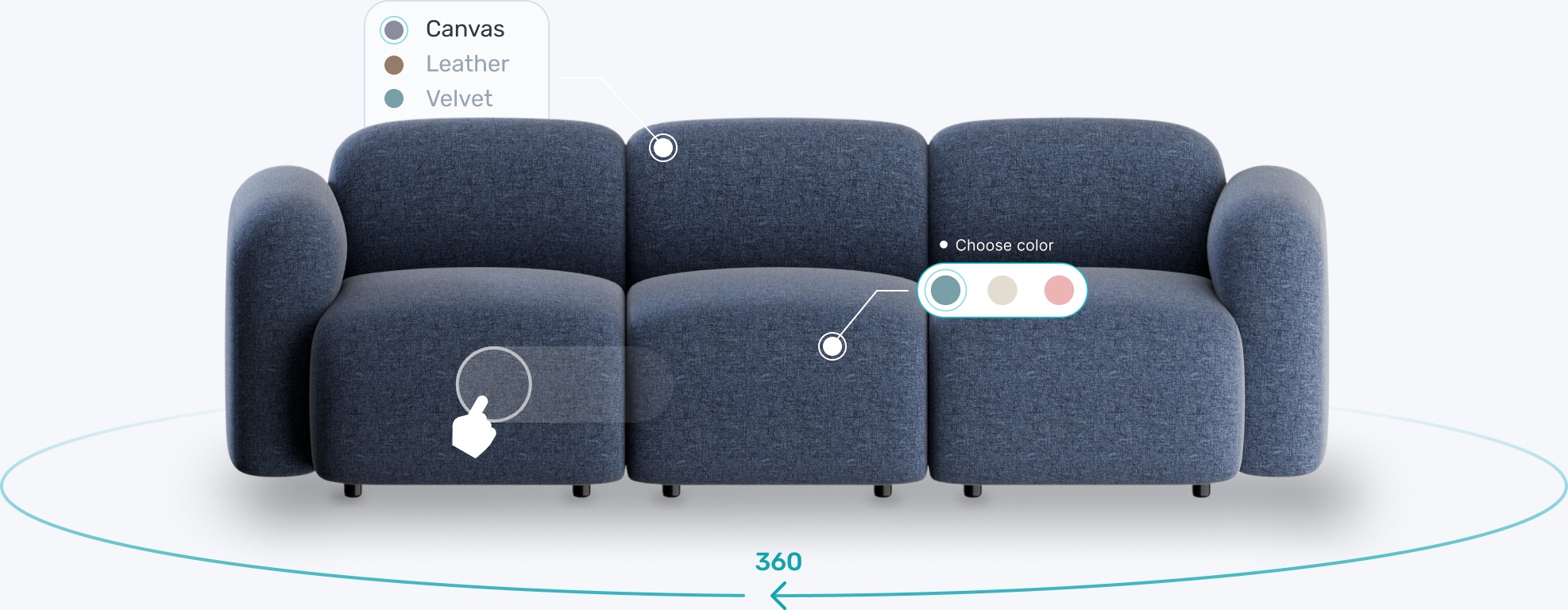
Quality assurance is a crucial part of the 3D modeling process. Customers need to know their assigned designer is building the most accurate portrayal of the model possible. It helps to have the option of providing feedback to smooth out any difficulties. That’s why Modelry provides an easy-to-use QA tool in its self-service platform.
Modelry’s QA system is a game-changer in the 3D modeling world. Customers have total control over the final result of their model, resulting in increased accuracy and a stress-free experience. Users can highlight areas of models that need work and suggest adjustments when needed. Customers can also leave comments for modelers telling them exactly what’s required.
Every order passes Modelry’s in-house quality assurance checklist. This covers core areas like shapes, textures, and materials. QA checkers ensure that models are realistic, closely match the reference files, and compare model outputs to project goals.
But what is the role of the customer in the QA process? Customer feedback really matters when fine-tuning models. So here are four helpful tips to guide your input and achieve the best possible results.
Comments to modelers can be as long as you like, but lengthy feedback isn’t usually a good idea. Try to keep comments relatively short and simple.
Simple language is easy to understand and translate into accurate models. As a rule, try to explain your requirements as if you were talking to a child. 3D modeling professionals won’t mind. In fact, they will welcome simple instructions.
Modelers want clear guidance about the actions they need to take. You can always add extra requests later on. Don’t overload modelers with information, otherwise your message could come off as convoluted.
At the same time, take care to describe your needs accurately. Use descriptive language that communicates your needs.
For instance, you might need a high poly car model with detailed reflections on the chassis. In that case, ask for a “more reflective” surface. Avoid general terms like “brighter”.
Good QA requires a methodical approach. Don’t leave out any requirements when interacting with modelers and be as thorough as possible. Remember: if you don’t make a request, your model may not be changed.
Provide enough feedback to make the changes required. If necessary, break down the QA feedback phase into different areas. Think about textures, proportions, colors, and materials. Make comments on each pinpointed area and send them to modelers if they need to make adjustments.
Align project goals with models in progress. Are your low poly furnishings realistic enough to populate a virtual reality environment? Do they need more work to fit your brand style?
Refine your models until your goals are met. That’s what the quality assurance system is for.
Sometimes text feedback is not enough. After all, creating custom 3D models is a visual task. Modelers need to have an image of the objects they are modeling. This is hard to achieve via text descriptions alone.
Modelry allows customers to provide visual feedback during the QA process. Alongside text suggestions, you could also supply a reference image to guide modelers as they make changes. Combining text and images is a great way to communicate details about texture, shape and color.
Customers can also supply contextual images to help modelers. For instance, if you are crafting AR experiences it might help to supply images of the spaces that 3D objects will occupy. If your brand has a particular visual style, images of similar 3D assets will be helpful.
Think beyond text. If you struggle to describe your requirements with words, images can be a much more effective option.
Modelry’s QA process is designed to deliver the best possible results for customers, and the results can be incredible. Take a look at our case studies for examples of AR-ready 3D furnishings, realistic 3D lifestyle scenes or interactive virtual 3D photography. Every customer can achieve similar outcomes.
However, sometimes users set their expectations too low. 3D technology is unfamiliar to many people. Customers may not realize how detailed and realistic models can be.
Low expectations lead customers to lower their requirements and accept imperfections. This should never be the case. Aim high and take time to communicate your goals via the QA system.
Spending a bit more time advising modelers will be worth it and time spent on QA is offset by time and cost savings elsewhere. Modelry lets you achieve impressive results without production delays. Our photorealistic modeling delivers big cost reductions compared to traditional photography.
Blend speed, value and quality by taking advantage of our QA tools. Whether you’re creating models for augmented reality apps or 3D viewers, cost effective modeling is within reach. Just follow our tips and Modelry’s quality assurance tools will make it easy to meet your modeling goals.